Neutralization Number (Acid / Base Number)
Understanding the Neutralization Number Test for Transformer Oil
The neutralization number, also known as the acid number, measures the amount of acidic substances in the transformer oil. It is expressed in milligrams of potassium hydroxide (KOH) required to neutralize the acid in one gram of oil. The test provides valuable information about the oil’s quality and helps in determining the need for maintenance or replacement.
Importance of the Neutralization Number Test
- Indicator of Oil Degradation: A higher neutralization number indicates a higher level of acidic compounds, which can result from the oxidation of the oil. This degradation can compromise the insulating properties of the oil and lead to the formation of sludge, which can obstruct oil flow and cooling.
- Maintenance Planning: Regular monitoring of the neutralization number helps in planning maintenance activities. If the neutralization number exceeds acceptable limits, it may be necessary to treat or replace the oil to prevent further degradation and potential transformer failure.
- Transformer Health: The test helps in assessing the overall health of the transformer. High acidity levels can lead to corrosion of metal parts and deterioration of the paper insulation, ultimately affecting the transformer’s performance and lifespan.
Testing Procedure
The neutralization number test is typically conducted using the following steps:
- Sample Collection: A representative oil sample is collected from the transformer.
- Titration: The sample is titrated with a standard solution of potassium hydroxide (KOH) using a suitable indicator to determine the endpoint of the reaction.
- Calculation: The amount of KOH required to neutralize the acid in the oil sample is measured and expressed in mg KOH/g of oil.
The acceptable limits for the neutralization number of transformer oil are generally as follows
- Good Condition: A neutralization number of 0.10 mg KOH/g or less is generally considered good and indicates that the oil is in good condition.
- Moderate Degradation: A neutralization number between 0.10 and 0.30 mg KOH/g suggests moderate degradation. It may be necessary to monitor the oil more frequently and consider treatment options.
- Severe Degradation: A neutralization number above 0.30 mg KOH/g indicates severe degradation. Immediate action, such as oil replacement or regeneration, is recommended to prevent damage to the transformer.
Several factors can influence the neutralization number of transformer oil:
- Oxidation: Exposure to oxygen can lead to the formation of acidic compounds.
- Contaminants: Ingress of moisture, dust, and other contaminants can accelerate oil degradation.
- Temperature: High operating temperatures can increase the rate of oxidation and acid formation.
The frequency of performing the neutralization number test on transformer oil can vary based on several factors, including the age and condition of the transformer, operating conditions, and the results of previous tests. However, here are some general guidelines:
- New Transformers: For new transformers, it’s advisable to test the oil within the first year of operation to establish a baseline.
- Routine Monitoring: For transformers in regular operation, conducting the test annually is a common practice. This helps in early detection of any degradation.
- Older Transformers: For older transformers or those showing signs of oil degradation, more frequent testing, such as every six months, may be necessary.
- After Maintenance or Repairs: If the transformer has undergone significant maintenance or repairs, it’s a good idea to test the oil shortly after to ensure no contaminants were introduced and the oil is still in good condition.
- Unusual Operating Conditions: If the transformer is operating under unusual conditions (e.g., high load, high temperature), more frequent testing might be warranted.
The neutralization number test is an essential part of transformer oil maintenance. By regularly monitoring the acidity of the oil, operators can ensure the reliable performance and longevity of transformers. Addressing high acidity levels promptly can prevent costly repairs and downtime, ensuring the efficient operation of electrical systems. If you have specific conditions or concerns, it might be beneficial to consult with a transformer maintenance specialist for tailored advice.
When the test results are out of acceptable range, Oil regeneration process might be needed to restore the properties of transformer oil, making it reusable and extending its service life. Here are some common methods of oil regeneration:
1. Vacuum Dehydration
This method removes water and gases from the oil by applying a vacuum. The oil is heated and then subjected to a vacuum, which causes the water and gases to evaporate. This process is effective in reducing moisture content and improving the dielectric strength of the oil.
2. Filtration
Filtration involves passing the oil through filters to remove solid contaminants such as dirt, metal particles, and sludge. This method helps in maintaining the cleanliness of the oil and preventing the formation of sludge that can obstruct oil flow.
3. Centrifugation
Centrifugation uses centrifugal force to separate contaminants from the oil. The oil is spun at high speeds, causing heavier particles to move outward and be collected separately. This method is effective in removing both solid and liquid contaminants.
4. Chemical Treatment
Chemical methods involve adding reagents to the oil that react with contaminants, such as acids and oxidation products, to neutralize or remove them. This process can restore the oil’s chemical properties and improve its performance.
5. Adsorption
Adsorption uses materials like activated clay or silica gel to absorb contaminants from the oil. The oil is passed through columns containing the adsorbent material, which traps impurities and allows clean oil to pass through. This method is particularly effective in removing polar compounds and oxidation products.
6. Reclamation
Reclamation is a comprehensive process that includes cleaning, drying, and adsorbing to remove color, acids, and sludge from the oil. It is a non-chemical process that restores the oil for reuse in the system.
7. Oil Clarification
This process involves removing aging products and restoring the structural composition of the oil. It typically includes steps like purification to remove water, gases, and mechanical impurities, and clarification to eliminate oxidation and aging products.
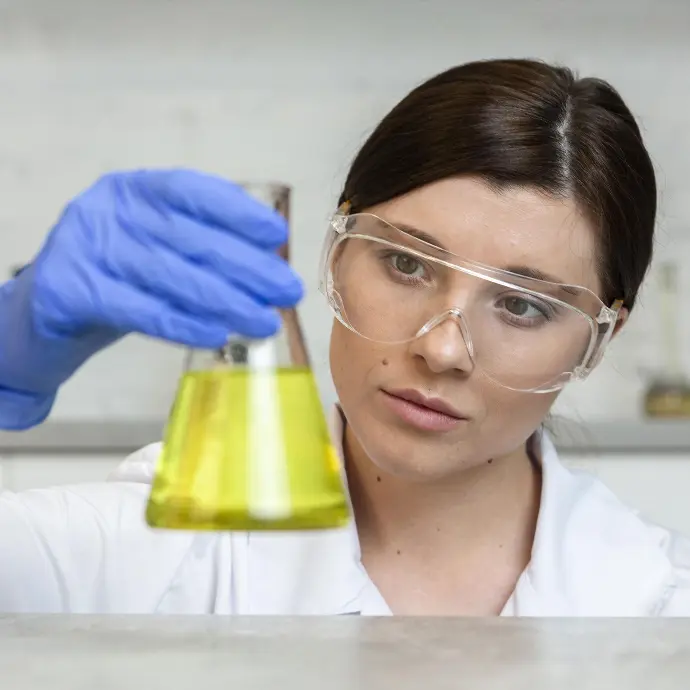