Dielectric Breakdown Voltage
ASTM D1816
Standard Test Method for
Dielectric Breakdown Voltage of Insulating Oils of
Petroleum Origin Using VDE Electrodes
Transformer oil, also known as insulating oil, plays a crucial role in the operation of transformers and other electrical equipment. It serves multiple purposes, including insulation, cooling, and protection against corrosion. One of the key properties of transformer oil is its dielectric strength, which is measured through the dielectric breakdown voltage (BDV) test.
The BDV test is essential for ensuring the reliability and safety of transformers. It measures the maximum voltage that the oil can withstand without breaking down. A high dielectric strength indicates that the oil is free from contaminants such as moisture, dirt, and other impurities, which can compromise the insulation and cooling properties of the oil.
Test Procedure
- Sample Collection: A sample of transformer oil is drawn from the transformer, typically from the bottom to ensure it is representative of the oil in use. The sample should be free from air bubbles and allowed to stand for about 20 minutes to let any trapped air escape.
- Preparation: The oil sample is placed in a test cell with two electrodes. The standard gap between the electrodes is usually 1 mm or 2 mm, depending on the specific test requirements.
- Testing: The voltage is gradually increased at a uniform rate (typically 500 V/sec) until the oil breaks down, causing a spark between the electrodes. The voltage at which this occurs is recorded as the breakdown voltage.
- Repetition: The test is usually repeated multiple times (often six) with the same sample to ensure accuracy. The average of these readings is taken as the final BDV value.
Interpretation of Results
- High BDV: A high breakdown voltage indicates that the oil is in good condition, with low levels of contaminants2.
- Low BDV: A low breakdown voltage suggests the presence of moisture, dirt, or other impurities. This can lead to reduced insulation properties and increased risk of transformer failure.
Transformer oil can be contaminated by various substances, which can significantly affect its performance and reliability. Here are some common contaminants:
- Moisture: Water is one of the most detrimental contaminants. It can enter the oil through leaks, condensation, or during maintenance. Even small amounts of moisture can drastically reduce the dielectric strength of the oil.
- Solid Particles: Dirt, dust, fibers, and other solid particles can enter the oil from the environment or during maintenance activities. These particles can provide a path for electrical discharge, reducing the oil’s insulating properties.
- Gases: Gases such as oxygen and nitrogen can dissolve in the oil. Oxygen, in particular, can lead to oxidation of the oil, forming acids and sludge that degrade its quality.
- Acids: Acids are formed as a result of the oxidation of the oil. They can corrode metal parts and further degrade the oil, reducing its effectiveness as an insulator and coolant.
- Sludge: Sludge is a by-product of oil degradation and oxidation. It can settle on transformer components, impeding heat dissipation and leading to overheating.
- Dissolved Metals: Metals such as copper and iron can dissolve into the oil from the transformer components. These metals can catalyze the degradation of the oil and reduce its insulating properties.
The frequency of BDV (Breakdown Voltage) tests on transformer oil can vary based on several factors, including the transformer’s age, operating conditions, and criticality. Here are some general guidelines:
- New Transformers: For new transformers, it’s recommended to perform an initial BDV test before commissioning to establish a baseline for future comparisons.
- Routine Maintenance: For transformers in regular operation, BDV tests are typically conducted annually. This helps in monitoring the oil’s condition and detecting any early signs of contamination or degradation.
- Critical Transformers: For transformers that are critical to operations or those operating under harsh conditions, more frequent testing (e.g., semi-annually or quarterly) may be necessary to ensure reliability and prevent unexpected failures.
- After Maintenance or Repairs: Whenever maintenance work is performed on a transformer, especially if the oil has been exposed to the atmosphere or if components have been replaced, a BDV test should be conducted to ensure the oil’s quality has not been compromised.
- Signs of Trouble: If there are any signs of transformer issues, such as unusual noises, overheating, or unexpected tripping, an immediate BDV test can help diagnose potential problems related to oil quality.
Regular BDV testing is crucial for maintaining the health and efficiency of transformers. It helps in early detection of contaminants and ensures timely maintenance, thereby extending the transformer’s lifespan and preventing costly downtime.
Oil regeneration, also known as oil reclamation, is a process designed to restore used transformer oil to a condition that is as close to new as possible. This process is crucial for maintaining the efficiency and longevity of transformers. Here’s a detailed look at the oil regeneration process:
- Dehydration: The first step involves removing water from the oil. Moisture can significantly reduce the dielectric strength of the oil, so it’s essential to eliminate it. This is typically done through vacuum dehydration, where the oil is heated under vacuum conditions to evaporate the water.
- Degassing: Dissolved gases, such as oxygen and nitrogen, are removed from the oil. This step is crucial because gases can lead to oxidation and other chemical reactions that degrade the oil.
- Filtration: Solid particles, including dirt, dust, and metal particles, are filtered out. This is usually done using fine filters that can capture even microscopic particles.
- Chemical Treatment: The oil is treated with chemicals to neutralize acids and remove oxidation by-products. This step helps in restoring the oil’s chemical properties and improving its performance.
- Adsorption: Adsorbent materials, such as activated clay or silica gel, are used to remove polar contaminants and degradation products. This step helps in clarifying the oil and restoring its insulating properties.
- Regeneration: The oil is passed through a series of processes to remove aging products and restore its original properties. This may include additional filtration, chemical treatment, and adsorption steps.
- Testing: After regeneration, the oil is tested to ensure it meets the required standards for dielectric strength, moisture content, acidity, and other parameters. This ensures that the regenerated oil is suitable for use in transformers.
Benefits of Oil Regeneration
- Cost-Effective: Regenerating oil is often more cost-effective than replacing it with new oil. It also reduces the need for disposal of used oil, which can be expensive and environmentally harmful.
- Environmental Impact: By regenerating oil, the environmental impact of oil disposal is minimized. This process helps in conserving resources and reducing waste.
- Improved Performance: Regenerated oil can perform as well as new oil, ensuring the transformer operates efficiently and reliably.
- Extended Transformer Life: Regular oil regeneration can extend the life of transformers by maintaining the quality of the insulating oil and preventing degradation of the transformer components.
In-Service Regeneration
One of the advantages of modern oil regeneration processes is that they can often be performed while the transformer is still in service. This minimizes downtime and ensures continuous operation of critical equipment12.
Various standards and guidelines specify the minimum acceptable BDV values for transformer oil. ASTM D1816 is followed for our BDV test. The International Electrotechnical Commission (IEC) recommends a minimum BDV of 30 kV for new transformer oil. Adhering to these standards ensures the safe and reliable operation of transformers.
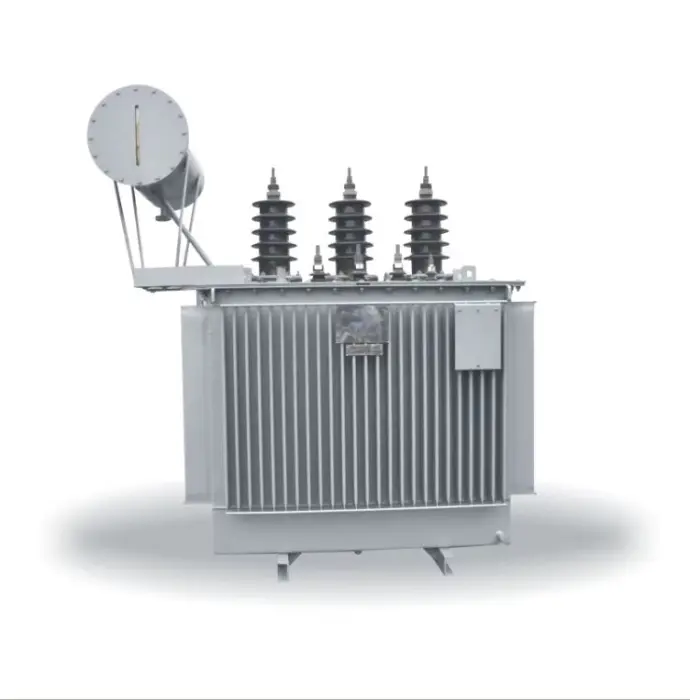