Oxidation Inhibitor Analysis
What are Oxidation Inhibitors?
Oxidation inhibitors are chemical additives that prevent the oil from reacting with oxygen, thereby slowing down the aging process of both the oil and the solid insulation within the transformer. The most commonly used oxidation inhibitors in transformer oils are 2,6-ditertiarybutyl para-cresol (DBPC), also known as butylated hydroxytoluene (BHT), and 2,6-ditertiary-butyl phenol (DBP). These inhibitors help maintain the oil’s dielectric properties and extend its service life.
Fourier Transform Infrared (FTIR) spectroscopy is a powerful analytical technique used to identify and quantify oxidation inhibitors in transformer oil. This method is standardized under ASTM D 2668 and IEC 60666. FTIR test allows for the precise determination of the total concentration of DBPC and/or DBP in the oil.
FTIR spectroscopy measures the absorption of infrared light by the oil sample. Each chemical compound absorbs infrared light at specific wavelengths, creating a unique spectral fingerprint. By analyzing these fingerprints, FTIR can identify and quantify the presence of DBPC and DBP. The detector measures the intensity of transmitted light at different wavelengths. The resulting spectrum is compared to reference spectra of known compounds. The concentration of oxidation inhibitors is determined by the intensity of their characteristic absorption peaks.
The Advantages of FTIR Spectroscopy are non-destructive as the sample remains intact after testing, and rapid and accurate. FTIR provides quick and precise measurements of inhibitor concentrations.
Interpreting FTIR spectra for oxidation inhibitors involves identifying specific absorption peaks that correspond to the chemical bonds in the inhibitors. Here’s a step-by-step guide to help you interpret these spectra:
- Obtain the Spectrum: Ensure you have a clear FTIR spectrum of the transformer oil sample. The spectrum will display absorption intensity versus wavenumber (cm⁻¹).
- Examine the Fingerprint Region:
- This region contains complex patterns unique to specific molecules. For oxidation inhibitors like DBPC and DBP, look for characteristic peaks at 3650 cm-1 and 860 cm-1 for DBPC, and 3650 cm-1 and 745 cm-1 for DBP according to ASTM D2668.
Compare with Reference Spectra:
- Use reference spectra of known oxidation inhibitors to match and confirm the presence of these compounds in your sample.
Quantify the Inhibitors:
- The intensity of the absorption peaks can be used to quantify the concentration of inhibitors. This is typically done using calibration curves obtained from known standards.
Here are some tips for the FTIR test:
- Baseline Correction: Ensure the spectrum is baseline-corrected to avoid misinterpretation of peaks.
- Peak Assignment: Assign peaks based on known functional group frequencies and compare with literature values.
- Software Tools: Utilize FTIR analysis software for more accurate peak identification and quantification.
Low inhibitor levels in transformer oil can lead to several noticeable signs, indicating that the oil is degrading and the transformer may be at risk. Here are some key signs to watch for:
1. Increased Acid Number
A rising acid number in the oil analysis indicates the formation of acidic compounds due to oxidation. This is a clear sign that the oil’s inhibitors are insufficient to prevent oxidation.
2. Sludge Formation
Sludge can form as a result of oil oxidation. It appears as dark, viscous deposits within the transformer and can be detected during oil sampling or visual inspections.
3. Decreased Interfacial Tension (IFT)
A drop in the interfacial tension of the oil suggests the presence of polar compounds, which are by-products of oxidation. Low IFT values indicate that the oil is losing its insulating properties.
4. Increased Moisture Content
Oxidation can lead to the formation of water as a by-product. Higher moisture content in the oil reduces its dielectric strength and can be detected through oil testing.
5. Darkening of Oil
The oil may become darker in color as it oxidizes and forms degradation products. This can be observed visually or through oil color tests.
6. Increased Dissolved Gas Levels
Dissolved gas analysis (DGA) may show elevated levels of gases such as carbon dioxide (CO₂) and carbon monoxide (CO), which are indicative of oil and paper insulation degradation.
7. Reduced Dielectric Strength
The dielectric strength of the oil may decrease, making it less effective as an insulator. This can be measured through dielectric breakdown voltage tests.
8. Higher Total Dissolved Solids (TDS)
An increase in total dissolved solids in the oil analysis indicates the presence of oxidation by-products and contaminants.
9. Increased Viscosity
The viscosity of the oil may increase due to the formation of high molecular weight oxidation products, affecting the oil’s flow properties.
10. Corrosion of Metal Parts
Corrosion of metal components within the transformer, such as the windings and core, can occur due to the acidic by-products of oil oxidation.
Maintaining an appropriate concentration of oxidation inhibitors is critical. Low levels of oxidation inhibitors in transformer oil can lead to several significant risks, impacting both the oil and the transformer’s overall performance. Here are the key risks associated with low inhibitor levels:
1. Accelerated Oil Degradation
Without sufficient oxidation inhibitors, transformer oil is more prone to react with oxygen. This reaction produces harmful by-products such as acids, esters, peroxides, moisture, and sludge. These by-products accelerate the aging process of the oil, reducing its effectiveness as an insulator and coolant.
2. Formation of Sludge
Oxidation by-products can lead to the formation of sludge, which can settle on the windings and other internal components of the transformer. Sludge buildup impedes heat dissipation, leading to overheating and potentially causing thermal degradation of the insulation.
3. Increased Acidity
As the oil oxidizes, it forms acidic compounds that increase the oil’s acid number. High acidity can corrode metal parts within the transformer, such as the windings and core, leading to electrical faults and reduced transformer lifespan.
4. Reduced Dielectric Strength
Oxidation by-products, including moisture and acids, can lower the dielectric strength of the oil. This reduction compromises the oil’s ability to insulate electrical components, increasing the risk of electrical discharges and failures.
5. Insulation Degradation
The solid insulation (typically cellulose-based) within the transformer is also affected by the by-products of oil oxidation. Acids and moisture can degrade the cellulose insulation, reducing its mechanical strength and increasing the likelihood of insulation failure.
6. Increased Maintenance and Operational Costs
Transformers with low inhibitor levels require more frequent maintenance and oil processing to remove oxidation by-products and restore oil quality. This increases operational costs and can lead to more frequent outages and repairs.
7. Risk of Transformer Failure
Ultimately, the combined effects of accelerated oil degradation, sludge formation, increased acidity, reduced dielectric strength, and insulation degradation can lead to transformer failure. This can result in costly downtime, repairs, and potential safety hazards.
To mitigate these risks, it is essential to regularly monitor the inhibitor levels in transformer oil and reinhibit the oil when necessary. Maintaining an inhibitor concentration of around 0.3% by weight is recommended to ensure adequate protection against oxidation. When the inhibitor level drops below this threshold, it is recommended to re-inhibit the oil, bringing the concentration up to around 0.3%. Reinhibiting involves adding fresh inhibitor to the oil. This process typically includes:
- Heating and Circulating the Oil: The oil is heated and circulated through adsorbent materials like Fuller’s Earth or activated alumina to remove old inhibitors, acid precursors, and other contaminants.
- Adding Inhibitor: A concentrated solution of DBPC is added to the oil stream returning to the transformer. The process is monitored to ensure the moisture content remains below 10 ppm.
Additional Considerations
- Oil Preservation Systems: Some transformers are equipped with systems designed to keep dissolved oxygen levels low, such as active nitrogen systems or conservator tanks with rubber diaphragms. While these systems reduce the need for inhibited oil, having inhibited oil provides additional protection in case of system failure.
- Acid Number and Interfacial Tension (IFT): If the acid number of the oil rises to 0.06 mg KOH/g or higher, or if the IFT drops to 31.9 mN/m or less, additional oil processing may be necessary before reinhibiting.
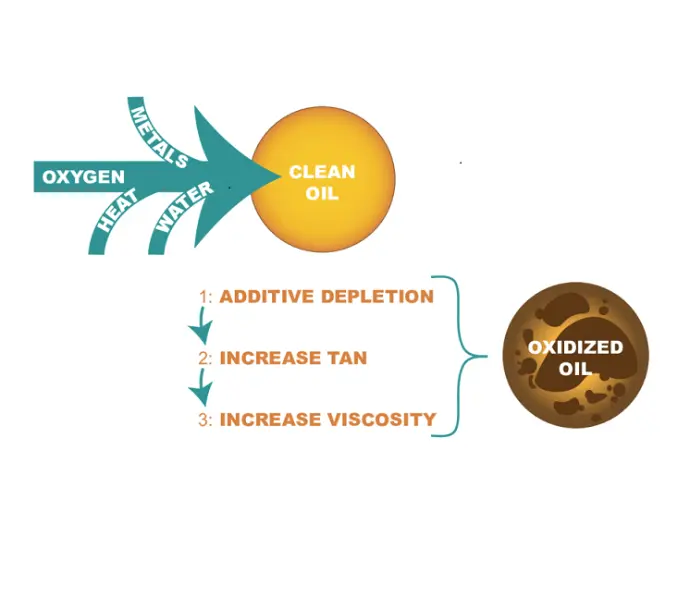